Using modeling to determine the best solvents for lignin product separations
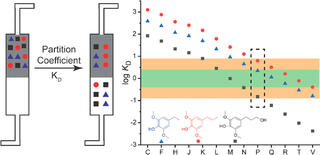
Application of existing methods and newly designed systems results in suitable solvent selections for the effective separation of aromatic lignin-derived products.
The Science
Lignin is an energy-rich and abundant component of biomass, accounting for up to 30% of lignocellulosic biomass by weight. Making valuable products from lignin is an important contributor to the economics of lignocellulosic biorefineries. Several depolymerization strategies have been developed to produce monomers from lignin. The separation of desired monomers from other lignin depolymerization products is necessary to facilitate their upgrading to valuable products. However, selecting the right solvent system to achieve that separation is often time-consuming and laborious. To alleviate that experimental burden, Great Lakes Bioenergy Research Center (GLBRC) researchers used computational methods to quickly and accurately identify optimal solvent systems for the liquid−liquid extraction of desired lignin monomers produced by four currently used depolymerization strategies.
The Impact
Selection of an optimal solvent system for efficient isolation of desired lignin monomers from a mixture can be a substantial experimental burden. The GLBRC team applied a computational model to calculate partition coefficients for four standard lignin depolymerization strategies in standard solvent systems. Based on their calculations, the team also designed new solvent systems expected to further improve separation efficacy. This computational approach greatly reduces the time and experimental burden required to select an optimal solvent system and has applications in other parts of the biofuels pipeline.
Summary
Due to the complexity of lignin structures, depolymerization produces mixtures of liquid-phase products. The separation of desired monomers from this mixture is necessary to facilitate their upgrading to valuable products and upscaling for industrial applications. One effective method to separate multiple liquid-phase products is countercurrent chromatography (CCC), which is a common liquid chromatography technique that separates target solutes based on differences in their partitioning in a biphasic solvent system. Effective CCC separation requires the selection of the right solvent system. To alleviate the experimental burden of selecting optimal solvent systems, GLBRC scientists applied the conductor-like screening model for real solvents (COSMO-RS) method to compute partition coefficients of lignin monomers from four currently used depolymerization strategies in standard solvent systems. They also designed new solvent systems that are predicted to further improve separation efficacy. On the basis of these predicted partition coefficients and empirical solvent selection criteria for CCC measurements, they suggested a range of solvent systems that would be suitable for the effective separation of aromatic lignin-derived products via CCC or similar liquid-liquid extraction methods. This computational approach can be applied to new lignin depolymerization mixtures to expedite lignin valorization efforts.
Program Manager
N. Kent Peters
kent.peters@science.doe.gov, 301-903-5549
Corresponding Author
Reid C. Van Lehn
vanlehn@wisc.edu
Funding
This material is based upon work supported by the Great Lakes Bioenergy Research Center, U.S. Department of Energy, Office of Science, Office of Biological and Environmental Research under Award No. DE-SC0018409. This work used the Extreme Science and Engineering Discovery Environment (XSEDE), which is supported by National Science Foundation Grant No. ACI-1548562.
Publications
Shen, Z. & Van Lehn, R. C. “Solvent selection for the separation of lignin-derived monomers using the conductor-like screening model for real solvents.” Industrial & Engineering Chemistry Research 59, 7755-7764 (2020). [DOI: 10.1021/acs.iecr.9b06086]
Related Links
- Link to the publication: https://pubs.acs.org/doi/10.1021/acs.iecr.9b06086
- Link to Q&A with Reid Van Lehn: https://www.glbrc.org/news/computational-modeling-faster-easier-separation-liquid-product-mixtures-qa-reid-van-lehn