Hydrogenolysis offers an improved method to break down lignin
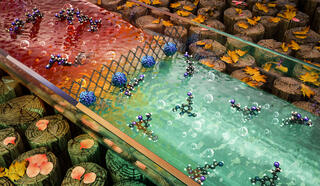
In combination with biomass pretreatment, the method produces lignin-derived monomers at yields near the theoretical maximum.
The Science
Lignin, an abundant component of plant cell walls, is a rich potential source of bioenergy but is extremely difficult to break down without significant degradation. Lignin isolated from commercial processes – such as from the paper and pulp industry – is mostly shunted to low-value uses such as being burned for heat.
In a new study, researchers at the Great Lakes Bioenergy Research Center (GLBRC) and the University of Wisconsin–Madison describe a lignin digestion method that can be coupled with existing biomass treatment processes to yield high levels of lignin-derived monomers, which can serve as feedstock for a wide range of industrial processes.
The Impact
Efficient lignin utilization has been identified as a key aspect of making biorefineries economically viable as alternatives to fossil fuel refineries. This study outlines a promising way to break down lignin into usable monomers with high yield. In addition, the researchers show that the method can be integrated with current biorefinery processes to produce lignin-derived compounds in parallel with existing product streams.
Summary
During traditional biomass processing, the harsh methods used to separate lignin from other components of the biomass can destroy the native lignin structure, leaving the material unsuitable for additional processing. In the new study, GLBRC researchers explored hydrogenolysis in a continuous-flow reactor, using lignin produced from biomass pretreatment methods developed by the GLBRC, as a way to improve lignin depolymerization on an industrial scale.
The researchers first used two model lignin compounds of predefined composition to evaluate the kinetics and mechanisms of hydrogenolysis in the continuous-flow reactor. Those model compounds helped identify reaction parameters, including reaction temperature, pressure, and flow rate, that suppressed formation of unwanted byproducts and maximized monomer yield. Next, they applied these parameters to lignin that was isolated from poplar wood chips using three different biomass pretreatment processes: mild acidolysis, gamma-valerolactone (GVL), and copper-catalyzed alkaline hydrogen peroxide (Cu-AHP).
The continuous-flow system enabled reaction parameter optimization in real time and produced monomer yields close to the theoretical maximum from the pretreated lignin. In addition, the structure of the unreacted lignin remained intact, allowing the material to be recycled through the reactor and reducing carbon loss into unusable byproducts. Combining a continuous-flow reactor with biomass treatment processes could enhance the yield and value of biorefinery products.
Program Manager
N. Kent Peters
Program Manager, Office of Biological and Environmental Research
kent.peters@science.doe.gov, 301-903-5549
Corresponding Authors
John Ralph
University of Wisconsin–Madison
jralph@wisc.edu
Jim Dumesic
University of Wisconsin–Madison
jdumesic@wisc.edu
Funding
This work was supported by the DOE Great Lakes Bioenergy Research Center (DOE BER Office of Science DE-SC0018409).
Publication
Y. Li et al. “Kinetic and mechanistic insights into hydrogenolysis of lignin to monomers in a continuous flow reactor.” Green Chemistry (2019). [DOI: 10.1039/c9gc00986h]
Related Link
https://pubs.rsc.org/en/content/articlelanding/2019/gc/c9gc00986h#!divAbstract