Oxygen-permeable membrane reactor offers scalable approach to lignin depolymerization
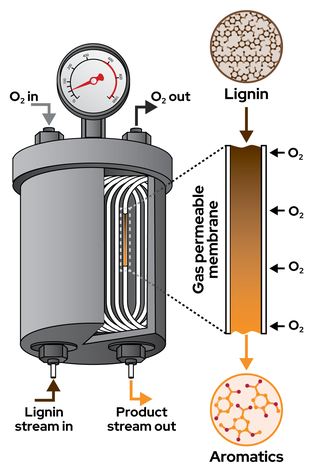
Background/Objective
Lignin is the world’s largest source of renewable aromatic compounds, but its heterogeneous composition and sequence that varies by source make it difficult to use as a chemical feedstock. Oxidative depolymerization methods generate valuable aromatic products, but such processes are difficult to control because reaction conditions that support depolymerization also contribution to product decomposition.
Approach
Researchers passed an alkaline aqueous lignin solution through gas-permeable tubing contained in a vessel filled with pressurized oxygen (O2) that rapidly heats the solution to 200 degrees C. The flow reactor allows for continuous oxygen delivery to the lignin solution and precise control of temperature and reaction time. The process was applied to hardwood and softwood lignin derived from different biomass pretreatment methods, including commercially-sourced kraft lignin.
Results
Reaction time-course analysis provides direct insights into the rates of lignin depolymerization and monomer decomposition, enabling process optimization. Aromatic yields up to 43 wt% are observed with a residence time of less than 4 minutes.
Impact
Conversion of waste materials into value-added products will play a crucial role in reducing dependence on fossil-derived chemical feedstocks. Lignin is currently a waste product derived from biomass processing, but it is the largest renewable source of aromatic chemicals. Using an O2-permeable membrane flow reactor limits the quantity of dissolved O2 present during the reaction and enables acquisition of valuable kinetic data that provide a foundation for development of larger scale processes.