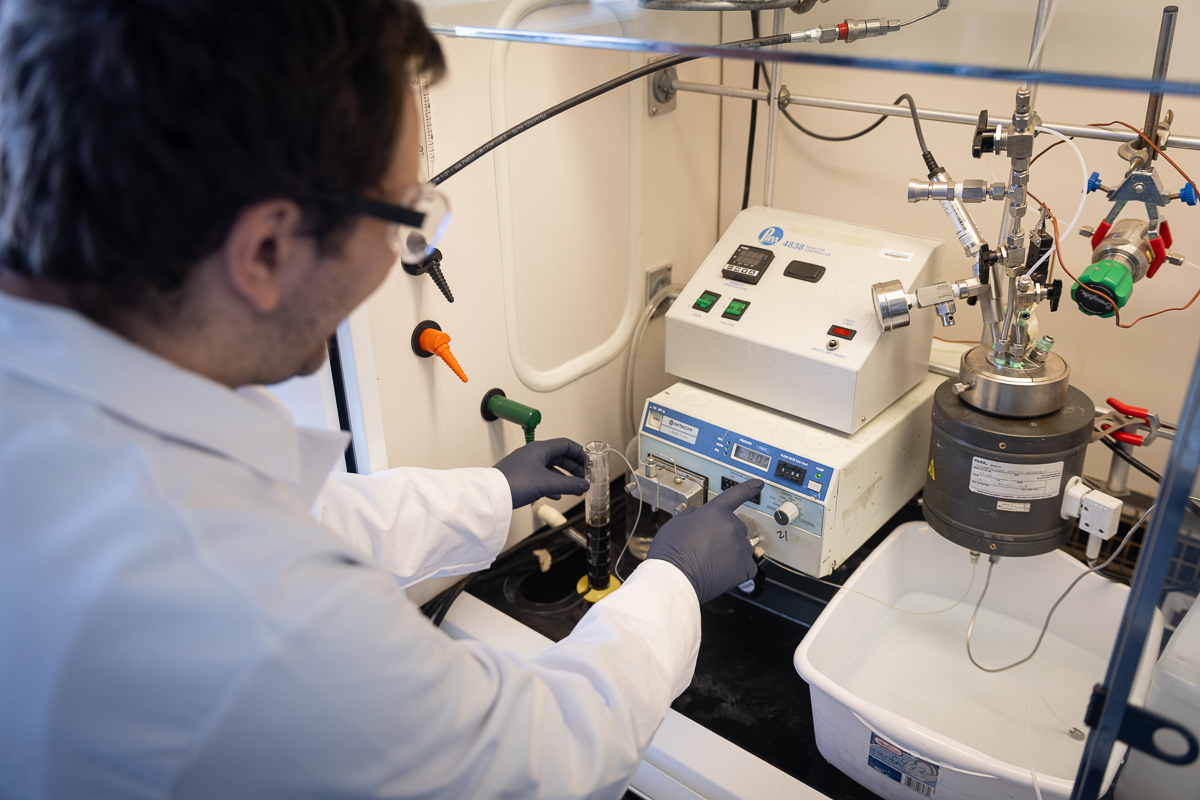
University of Wisconsin–Madison researchers have developed a new process that could help make plant-based plastics and other alternatives to fossil fuels more economically viable.
Led by chemistry professor Shannon Stahl and chemical engineering professor Thatcher Root, a team of researchers with the Great Lakes Bioenergy Research Center used oxygen to break down a tough form of plant fiber called lignin into chemicals that resemble the building blocks of many plastics and textiles currently made from petroleum.
Stahl said the findings, detailed in the journal Joule, represent an important step in the fight to slow climate change.
“We need to find practical alternatives to fossil carbon sources, and biomass is an ideal target because it is made by removing carbon dioxide from the atmosphere,” Stahl said. “The bottleneck right now is translating lab-scale methods to scalable applications, and this work is an important advance toward this end.”
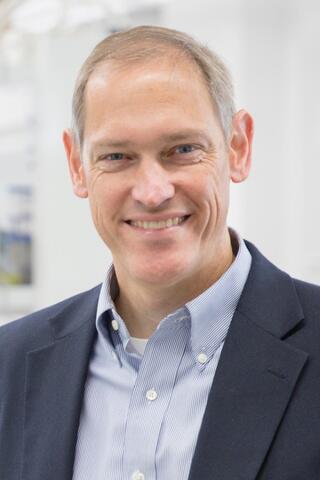
The goal is to use lignin to produce valuable aromatic chemicals – hexagonal molecules such as benzene, toluene, and xylene – that are currently derived from petroleum as part of the refining process.
Lignin, a polymer – or chain of molecules – that binds together sugars and provides structure to plants, is the world’s most abundant natural source of aromatics. But industries like paper mills and biorefineries typically burn it for heat because the irregular structure and variability make it hard to break down into useful parts.
Stahl likens lignin to fabric in which the aromatic rings are connected with chemical “threads.” Oxygen removes electrons from the atoms in the threads, weakening the connections until the thread frays and releases the aromatic rings.
The chemistry has been known for decades, Stahl said. What sets this work apart is the way it was applied.
The team designed a reactor that pumps an alkaline lignin solution through gas-permeable tubing in a tank filled with pressurized oxygen that rapidly heats the solution to 200 degrees C and then cools the product stream that comes out the other side.
Because the process is continuous, the aromatic products can be removed before they start to degrade, as they would in a batch reactor.
And continuous biomass processing will be key for competing with existing oil refineries.
“If we’re really going to replace petroleum ... we need an economically viable biorefinery,” Stahl said. “The problem is that many breakthroughs need to happen at the same time for this to work. And it has to be cost effective.”
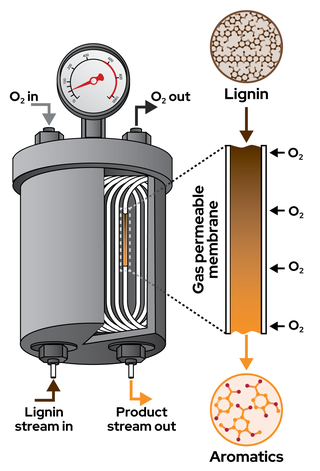
The reactor produced impressive yields of aromatics within minutes from both hardwood and softwood lignin as well as the messier kraft lignin produced by pulp and paper mills.
Once the lignin polymer is chopped up, the aromatic molecules can be fed to genetically-engineered microbes that convert them into valuable products. One appealing target is muconic acid, a chemical that can easily be turned into adipic acid, one of the primary ingredients used to make plastics and textiles.
One of the advantages to using an oxidation process is the resulting molecules dissolve better in water, making it easy to feed them to the microbes. Other methods of depolymerization produce oily feedstocks that don’t mix as well with water.
Stahl’s lab is now working to scale up the process, first to 1-kilogram and then 10-kilogram scale by next year in as part of a federally-funded project that combines science, art, and policy to make plant-based plastics from paper mill waste in ways that benefit marginalized communities.
Stahl said what sets the project apart is the new reactor design allows scientists to gather data that will help improve the process at larger scales.
“Because of the engineering, we can actually learn about the chemistry in ways that we couldn’t otherwise,” Stahl said. “The reactor provides exquisite control over the process, allowing us to fine tune the chemistry that’s happening in this very complex process.”
At the same time, Stahl is working to develop a continuous process to further refine the aromatics by separating individual molecules from waste products.
“Once we do that, we would be equipped to deliver the basic building blocks that anybody could use for an array of industrial applications,” Stahl said. “We will have basically converted this waste product into a useful building block stream.”
Financial support for this project was provided by the Great Lakes Bioenergy Research Center, U.S. Department of Energy, Office of Science, and Office of Biological and Environmental Research.