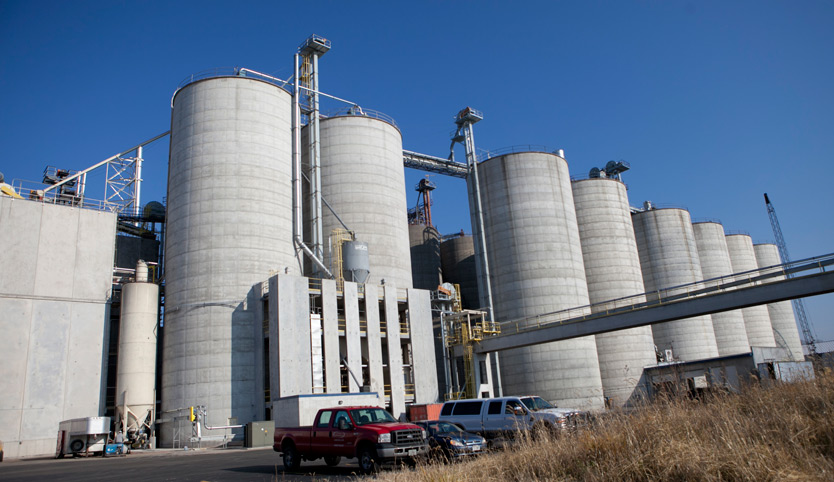
When a 100-ton supply of feedstock arrives at the biorefinery of the future, the plant manager could open the door to find cellulosic biomass in any number of forms — from corn stover to switchgrass to poplar or miscanthus or mixed prairie grasses and forbs.
Researchers at the Great Lakes Bioenergy Research Center (GLBRC) are working to ensure that these biorefineries will have the tools they need to tackle whatever feedstock arrives at their gate.
These tools will include the two pillars of biomass processing: pretreatment mechanisms and enzyme cocktails. Together they can be leveraged to maximize the release of fermentable sugars from cell walls. Since enzymes are a major contributor to fuel processing costs, GLBRC researchers are working to create customized enzymes that can beat the current one-size-fits-all commercial enzyme approach. By using enzyme cocktails that are tailored to specific pretreatments and feedstocks, enzyme loading—or the ratio of protein to feedstock—is reduced, and with it processing cost.
A robotic tool called GENPLAT, short for GLBRC Enzyme Platform, allows scientists to develop customized enzyme mixtures on the fly. GENPLAT is a high-throughput digestion platform that combines robotic liquid handling, statistical experimental design, and automated assays that measure glucose and xylose levels.
Biofuels experts predict that advanced biofuels will be generated from a variety of biomass feedstocks with very different structural characteristics; hence the need for robust enzyme cocktails tailored to different feedstocks.
In the current landscape of biofuels processing, commercial enzymes are a mixed bag.
“Right now, all the commercial enzymes are complex undefined mixtures of more than 100 proteins,” says Jonathan Walton, associate director of Great Lakes Bioenergy Research Center for Michigan State University.
Through his work with the GLBRC, Walton’s goal is to create custom enzyme mixtures that are more effective than commercial varieties, which are expensive and generally optimized for acid-based pretreatment approaches.
“Enzymes are expensive,” Walton says. “So we’re trying to figure out what is really needed.”
With the ability to rapidly screen enzymes for effectiveness, Walton’s group is turning their focus to discovering new enzymes that could help bolster glucose release.
“So far we can match the commercial enzymes, but we have a lot of potential to continue to make them better,” Walton says. “We’re working on another 10 that we hope will make a difference.”
As other scientists at the GLBRC identify new and better enzymes through bioprospecting in natural environments such as cow rumen and other cellulose-rich environments, and by protein engineering, these enzymes can be tested and added to the mix.
“In the future, a biorefinery could run their feedstock though GENPLAT and come up with a custom enzyme cocktail for how to break it down most efficiently.”